

-
Mandrel tube piercing tool punches multiple diameter of round aluminum tubes / channels. Changing tools for different sizes over time is eliminated because one tool has all sizes that the operation needs.
-
Hole / slot positions are close to the end of tube.
-
Punches clean holes / slots in the tube. Then the tube is rotated to punch an other hole at 90 degree with a help of a special pin. Repeat process until there are all four sides of the tube has been punched.
Call: 1-604-239-7218 | info@vortool.com
Made in Canada.


Mandrel tube / pipe piercing tool
Made to order
This mandrel pipe / tube slot punching tool and die has three different stations for punching 1-4 slots in aluminum pipes, tubes or channels.
Special punching applications require processing other than flat sheet metal parts.
Tubes can be punched in many different ways, e.g. punching slots on the surface of a tube. In this example there are three different diameter tubes. All has the same slot sizes and each slot is equally spaced at four locations, opposite to each other. So, a tube must be punched 4 times by rotating the tube after each hit or punched slot. The 90 degree rotation is important at this case.
To punch the slots in the tube, we need a mandrel metal stamping tooling. The tooling has three mandrels. In this case the mandrels are the die plates with the die cavity. The metal stamping tooling also has the three punches that would punch the slots in the tubes. The punch must slide up and down, aligned with the die cavities below. To achieve that, the tool needs at least two guide pins and bushings that are part of the die set. Punching require a lot of force, so the mandrels must be rigid enough in the retainer block to withstand the force and not bending or braking off.
Once the slot is punched in the aluminum tube, the scrap or called slug, will fall down and once the tube is pulled off the mandrel, the slug can freely exit. In order to punch three more slots in the same tube, precisely positioned 90 degree from each other, a locator device is required. This device is a spring loaded ball that is positioned at one side of the mandrel, precisely 90 degrees from the die cavity. Once the 1st slot is punched, the tube can be rotated. The existing slot should be rotated toward the spring loaded ball. Once in close proximity, the ball snaps into the tube's existing slot from the inside. It snaps it to position. The new slot then can be punched. Repeat this two more times and all 4 slots will be accurately punched into the same tube. The result is as good as it can get. Slots are perfectly spaced, and have smooth outer punched edges and bur free inside edges around the perimeter of the slots.
You also need a power source that drives the tool's upper unit up and down with enough force to punch the slot into the tubes. In this case 5 tons was needed to punch one slot. A special air over oil cylinder portable press station was designed and built that is perfectly suited for this application. The press frame had to be just small enough for the tool to save space, but powerful enough to do the job efficiently. This air over oil cylinder portable press station entirely relies on compressed air only (regular shop air). The output of the cylinder in this press is 7.5 tons that is more than enough for punching these slots. The cylinder is an air to oil unit that has the rigid brute force of a hydraulic cylinder, but has the speed of an air cylinder The press can cycle about 40 times a minute.

Portable mandrel tube / channel punching press station
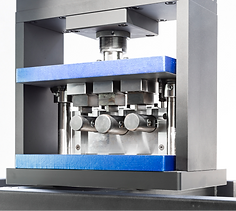

Mandrels holds aluminum tubes, so slots can be punched on 4 sides by turning them.
Unit could be easily relocated with a pallet jack.
Multi station mandrel tube piercing tool and press to punch clean holes / slots in aluminum channels.